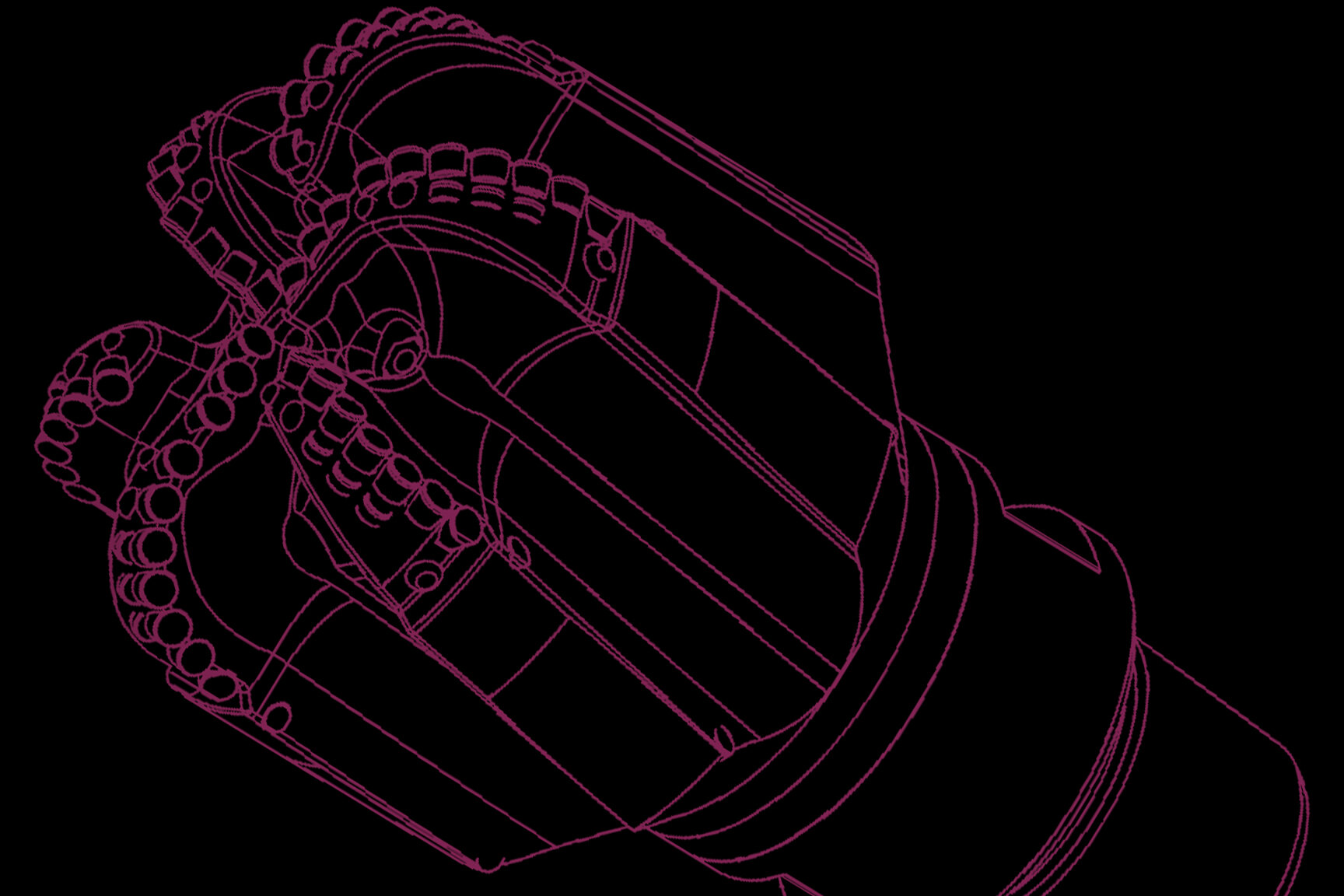
PDC Performance Chart
Honoring a commitment to research and development so that every PDC cutter we offer fills a customer need, including the latest developments in uniquely shaped cutter technology. All our cutters are field-tested and proven under various drilling conditions across the globe. We offer a variety of grades to address the most demanding requirements whether they be performance or economically driven.
Every cutter undergoes a rigorous inspection process to ensure consistency. In compliance with ISO 9001 quality standards, we institute a strict quality check process on every PDC (polycrystalline diamond) cutter we sell.
Every new product we develop is a response to the question “how does this fit into our customer’s needs”. With the ever-changing financial stresses in the market, we understand that it is essential to develop products that will not only perform but will also deliver an economical value for our customers. Through relentless research and development efforts, we have developed three new product series: All-Terrain, Tactical, and Elite. These series utilize our proprietary press methods to provide enhanced, customizable PDC Cutters to cover multiple facets of hard-to-drill environments.
All-Terrain Series is designed to economically tackle three key performance aspects: thermal, abrasion, and impact. The delicate balance between these three characteristics is crucial to how the products in this series perform downhole. Consider this series as an asset to your overall PDC needs.
The design idea behind our Tactical Series was to develop products that are focused on specific performance requirements for niche drilling environments. Some applications require a cutter with exceptional thermal resistance while others require higher abrasion resistance or toughness characteristics. This series puts an emphasis on specific aspects of those thermal, abrasion or impact resistance needs in certain drilling applications.
Our premium series was designed to answer the call for your most demanding applications. Utilizing our proprietary press method, and with extensive lab and field testing behind it, these cutters have demonstrated extreme thermal stability, along with exceptional toughness and resistance to wear. Each test revealed the highest level of performance your application might require in order to be considered “Elite”. This is truly the pinnacle of PDC.
Shaped Cutters
The standard PDC cutter cylinder is not the only shape for cutters on the market today. Shaped PDC cutters are evolving in every aspect of the drilling arena. Whether you are looking for increased ROP, optimized cooling, better depth of cut and formation engagement, or better secondary cutting elements. We can provide a shape that can perform in any number of applications and requirements. Our engineering team has designed a wide variety of shapes that succeed in offering exceptional performance in any number of challenges that downhole drilling can present.
In addition to offering IDS’s unique shaped cutter designs, we also collaborate with our customers to develop mutually designed shapes or to build designs developed by them.
Thermally Stable
Our engineering team, through extensive development efforts, has succeeded in designing thermally stable PDC cutters for the general market that allows any PDC Bit company the ability to compete in the most challenging applications that the industry could present. Utilizing proprietary manufacturing techniques coupled with IDS’s superior processing capability we were able to offer game-changing technology that opened the market for many of our customers. IDS has continued to build on these product designs to improve their performance in keeping with the growing demand for long life and thermal stability for PDC cutters in the market.